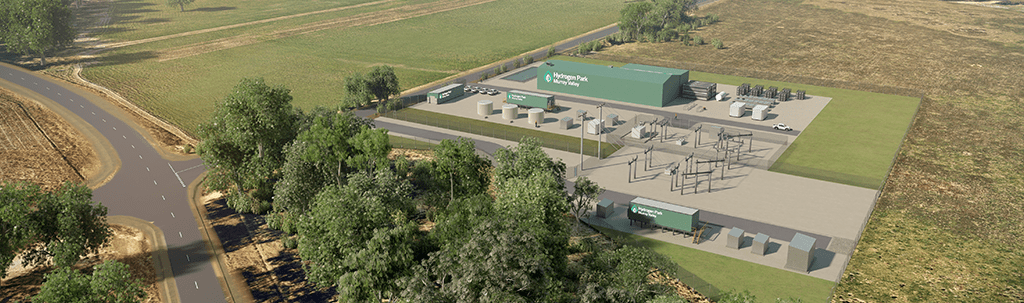
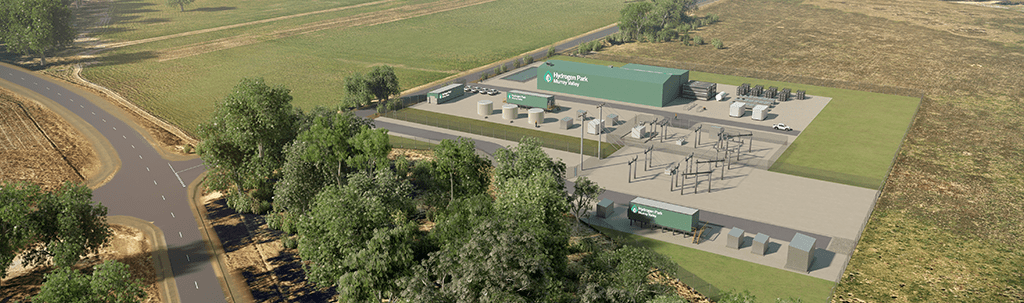
In hydrogen fuel cells, electrolyte membranes frequently undergo deformation and develop cracks during operation. A research team has recently introduced a fatigue-resistant polymer electrolyte membrane for hydrogen fuel cells, employing an interpenetrating network of Nafion (a plastic electrolyte) and perfluoropolyether (a rubbery polymer). According to the study, the innovation will not only improve fuel cell vehicles but also promises advancements in diverse technologies beyond transportation, spanning applications from drones to desalination filters and backup power sources.
Hydrogen fuel cells contain a polymer electrolyte membrane that serves as a barrier between the electrodes (the conductors that enable the flow of electricity through a substance). This membrane conducts protons but inhibits the movement of electrons, hydrogen molecules, and oxygen molecules.
When a vehicle speeds up or slows down, the fuel cell operates inconsistently, leading to varying water production and causing the membrane to expand and contract. The repetitive deformation over time results in the formation of cracks, accelerating the undesired transport of hydrogen through the membrane and ultimately causing operational failure. Some methods employed to address these cracks include radical scavengers and hydrocarbon electrolyte membranes. However, while these approaches offer some defense, they are not capable of entirely preventing the formation and propagation of these cracks.
In a study published in the journal Advanced Materials on December 31, 2023, led by Associate Professor Sang Moon Kim from Incheon National University and Professor Zhigang Suo from Harvard University, a team of researchers has developed a polymer electrolyte membrane that is resistant to fatigue. “To ensure the long-term stable operation of fuel cells, it is essential to develop an electrolyte membrane with high resistance to repetitive fatigue failure that reflects the actual operating environment and degradation process of fuel cells,” said Kim. “In our study, we utilized an interpenetrating network to intentionally distribute repetitive stress.”
The researchers created a category of fatigue-resistant electrolyte membranes, consisting of an interpenetrating network of Nafion and perfluoropolyether (PFPE). Nafion is a commonly used plastic electrolyte with proton-conducting properties, while PFPE creates a durable, rubbery polymer network. The incorporation of the rubber slightly diminishes electrochemical performance but markedly enhances fatigue threshold and lifespan.
The membranes had varying levels of PFPE, and among them, the one with 50% saturation exhibited reasonable electrochemical performance. In comparison to the original Nafion, this Nafion-PFPE membrane elevates the fatigue threshold by 175% and extends the lifespan of the fuel cell by 1.7 times. Additionally, the unmodified Nafion membrane exhibits a lifespan of 242 hours, whereas the composite membrane was observed to have a lifespan of 410 hours. These results collectively suggest that incorporating the rubbery network modestly reduces electrochemical performance but significantly improves fatigue resistance and overall lifespan.
The researchers believe that the study holds considerable significance across diverse applications. The introduction of a fuel cell system with stability, durability, and performance has the potential to pave the way for innovations in various industries. Beyond the realm of fuel cell vehicles, it can impact the development of advanced technologies in drones, personal air vehicles, backup power sources, forklifts, bicycles, scooters, and more.
“Furthermore, the strategy for enhancing fatigue resistance can be extended and applied to ion filters, battery separators, and actuation systems. This allows for broad application in high-durability, long-life desalination filters, flow battery separators, lithium metal battery separators, and artificial muscles,” said Dr. Kim.
About The Authors
Prof. Zhigang Suo is the Allen E. and Marilyn M. Puckett Professor of Mechanics and Materials at Harvard University. He earned a Ph.D. in Engineering Science from Harvard University in 1989. His research centers on the mechanical behavior of materials and structures. Basic processes include fracture, deformation, polarization, and diffusion, driven by various thermodynamic forces.
Prof. Sang Moon Kim is an associate professor in the Department of Mechanical Engineering at Incheon National University in South Korea since 2016. He received his Ph.D. from the School of Mechanical and Aerospace Engineering at Seoul National University in 2015. His research interests include multiscale design and fabrication of membrane and electrode architectures for fuel cell and filtering systems.
References
Authors: Minju Kim1, Guogao Zhang2, Segeun Jang3, Sanghyeok Lee3, Zhigang Suo2,*, and Sang Moon Kim1,*
Title of original paper: Fatigue-resistant Polymer Electrolyte Membranes for Fuel Cells
Journal: Advanced Materials
DOI: https://doi.org/10.1002/adma.202308288
Affiliations:
1Department of Mechanical Engineering, Incheon National University
2John A. Paulson School of Engineering and Applied Science, Harvard University
3School of Mechanical Engineering, Kookmin University
*Corresponding authors’ emails: ksm7852@inu.ac.kr (Sang Moon Kim), suo@seas.harvard.edu (Zhigang Suo)