
Leveling Up The Playing Field
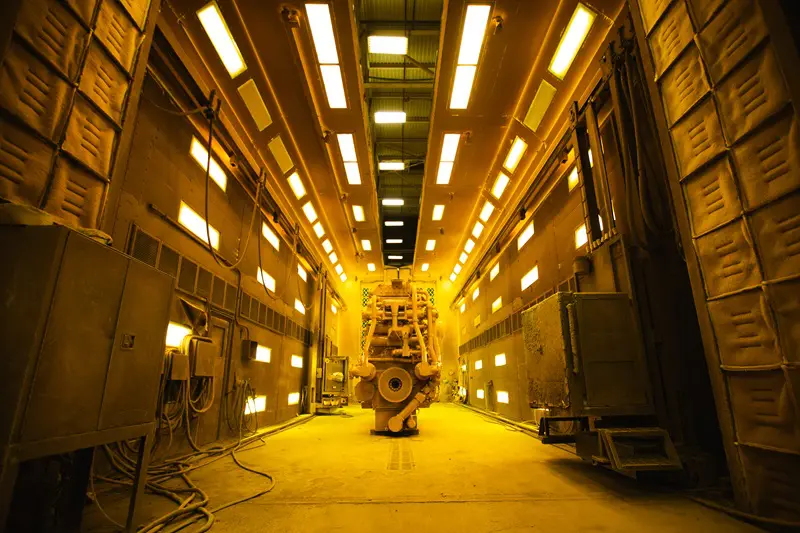
In September 2023, Caterpillar announced the second generation of the Cat G3600 A4 engine — the newest chapter of the G3600 series. The first generation of the G3600 A4 debuted in 2015, while the G3600 A3 engine dates back to the early 2000s. Compared to the G3600 Gen 1 model, the Gen 2 engine provides 6% to 8% lower greenhouse gas emissions, a 33% to 42% reduction in methane emissions, a 9.6% higher flow rate with an appropriately-matched compressor when running at full load, and an optional 10% increase in power that can lead to a 9.6% increase in gas production throughput. The G3600 Gen 2 engine is designed for up to 100,000 hours of operation before requiring a rebuild with recommended maintenance, making it the most durable Caterpillar gas compression engine to date.
Caterpillar followed up by announcing that Gen 2 upgrade kits are now available for G3600 A3 engines, not just G3600 A4 engines. Engines upward of 20-years-old have the potential to achieve similar methane and greenhouse gas (GHG) reductions as the G3600 A4 Gen 2 engine when upgraded with a Gen 2 kit. “The A3 engine population is going through a heavy overhaul cycle in 2024 and 2025, whereas the majority of the A4 engines that were put into service starting in 2015 have not hit their first in-frame and major overhaul,” said Darin Bohlmann, product manager at Caterpillar. “The Gen 2 upgrade requires new pistons and cylinder liners which are typically replaced at 50,000- and 100,000-hour increments. When performed at one of these overhauls, this upgrade is basically cost-neutral.”

(Image Courtesy Of Caterpillar)
The timing works out well given many G3600 A4 Gen 1 models are nearing their 50,000-hour overhaul, whereas the majority of the G3600 A3 engines are due for in-frame and major overhauls. The release of the new G3600 Gen 2 engine and Gen 2 kits opens the door to an emissions reductions opportunity for customers that were scheduled to overhaul their engines.
Tightening Emissions Requirements
According to the US Environmental Protection Agency (EPA), the Inflation Reduction Act (IRA) provides new authorities under Section 136 of the Clean Air Act to reduce methane emissions from the petroleum and natural gas industry through the creation of the Methane Emissions Reduction Program. The proposal includes various financial and technical assistance programs, funding opportunities, and administrative and legal requirements. The program also “establishes a waste emissions charge for methane from applicable facilities that report more than 27,558 tons [25,000 tonnes] of carbon dioxide equivalent [CO2e] per year to the Greenhouse Gas Reporting Program (GHGRP) petroleum and natural gas systems source category and that exceed statutorily specified waste emissions thresholds. Waste emissions charge starts at US$900 per metric ton for emissions reported in 2024, increasing to US$1200 for 2025 emissions, and US$1500 for emissions years 2026-on.” The EPA closed its comment period on October 2, 2023, for proposed regulations published on August 1, 2023. In addition to the waste emissions charge, the EPA will finalize new reporting rules by August 26, 2024, that will become effective January 1, 2025. There is talk that new rules will affect a larger portion of the energy sector than before, from pipelines, energy production companies, the gas production, compression, processing, transporting, and storage industry, and potentially even petroleum production facilities and the liquefied natural gas industry.
Regardless of what happens in 2025, the bigger issue is that there are growing direct environmental and economic costs to GHG emissions. There is also the indirect risk of being reactive rather than proactive toward environmental, social, and governance (ESG) objectives, which could damage a brand, employee retention, and all stakeholders over time.
Companies like Caterpillar are making product improvements, both from a hardware and software standpoint. Customers are able to improve output and throughput while lowering emissions in the process. “Our customers want to be more sustainable,” said Bohlmann. “But if your cost to move gas is higher than your competitors, that’s not economically sustainable. At Caterpillar, we are constantly working to meet increasingly tougher emissions regulations, while also delivering more value to the customer. In addition to the Gen 2 updates announced, we are continually working on the next generation emissions controls which will provide further methane reductions.”
The new horsepower that Caterpillar sells each year pales in comparison to the cumulative horsepower of its installed base. Roughly 5% of additional horsepower through new installations could be added to the installed base in a single year. “There’s just not a lot of attrition in the G3600 platform,” said Bohlmann. “That’s what Caterpillar is known for. You can drive down many of our highways and see some of the oldest-looking Cat machines out there that are still working and still have the parts and service to support it.” Upgrade kits are a key component of maintaining Caterpillar’s massive installed base of more than 8500 units operating in the field. Although G3600 A3 engines can be upgraded to the G3600 A3 Gen 2 hardware set, engines dating prior to A3 do not apply and cannot be upgraded with a Gen 2 kit. Customers with multi-decade old engines can purchase new equipment to achieve their environmental targets.
A Better Value For Customers
According to Caterpillar, the company’s reliable aftermarket support and parts availability, combined with an engine’s long life, reduces operators’ total cost of ownership (TCO). “With the Caterpillar G3600 Gen 2, midstream gas compression companies can move more gas with fewer engines,” said Matt O’Sullivan, Caterpillar Oil & Gas general manager. “Companies are enabled to achieve their operational priorities while maintaining performance and efficiency.”

Caterpillar’s newest engine allows its customers to do more work with less equipment, while the Gen 2 upgrade kits are meant to sustain the life of equipment that has been a backbone of the gas compression industry for decades. Caterpillar can reduce costs for customers through both performance and emissions improvements. “We are constantly looking at the impact to TCO as we work to engineer more value into a product,” said Bohlmann. “The Gen 2’s lower emissions and optional 10% power increase with the A4 model is a good example.”
Maintenance and repair are also key ingredients in the G3600’s success. “The parts and service network for this product is second to none,” said Bohlmann. “Between the Caterpillar dealers, compression equipment original equipment manufacturers [OEMs], and fleet operators, there’s an established network of spare parts, engines, and certified technicians to keep them running. We work hard to ensure they have the right tools, training, and parts needed to maintain our uptime.”
The New 80/20 Rule
The diesel version of the G3600 was introduced almost 40 years ago, and the gas compression version came out in 1991. For more than 30 years, Caterpillar has kept the G3600 relevant, reliable, and easily serviceable. Economics, emission reductions initiatives, and increased remanufacture ability undoubtedly drove the last 30 years of improvements to the G3600 product line. The question now is if economics and environmental compliance will lead the next 30 years of the G3600’s evolution, a time frame that includes the 2050 net-zero target that was announced by the United States in 2021.
Although Caterpillar doesn’t have a net-zero target, it does support the goals of the Paris Agreement to limit global temperature rise and is committed and contributing to a reduced-carbon future. In 2021, Caterpillar set seven new sustainability goals for 2030, including reducing absolute Scope 1 and 2 GHG emissions by 30% between 2018 and 2030. The company also set a goal that 100% of new products through 2030 will be more sustainable than the previous generation. Beginning in 2022, Caterpillar incorporated ESG performance into the incentive plan for executive officers. Caterpillar also publishes an annual sustainability report.
“Emissions reductions are driving a high percentage of our research and development investments on the G3600, in addition to other oil and gas product developments,” said Bohlmann. “As we look forward, I think this reality will continue. We know compression applications are converting to electric motors, and already, we are seeing compression being powered by gas turbines. We’re always working to get more power out of the same platform, but we know there’s no ‘one size fits all’ approach. As complex and sometimes unpredictable emission regulations grow, our focus on products and services will continue to evolve to maintain reliability.”
Regulatory changes can vary by industry. For example, the EPA’s non-road mobile diesel emissions requirements in the United States are fairly similar to requirements in Europe and Canada. China used to be a lesser regulated country but has more recently implemented similar standards on its diesel engines. “Stationary gas compression engines are regulated differently than mobile engines,” said Bohlmann. “They are not certified the way diesel engines are. They are site-certified by the operators, and there are unique requirements in different states and countries. For example, Canada’s carbon tax is driving some very unique emissions requirements. A universal approach is not possible when regulations vary so widely.”
Hydrogen Gas Compression’s Supply Constraint
Aside from making improvements to the G3600 line, another way Caterpillar is tackling emissions reductions is by embracing opportunities with hydrogen. “We’ve done a fair amount of testing on hydrogen blending,” said Bohlmann. “There is significant interest from our oil and gas customers including gas compression, well service, and drilling to meet regulatory standards. We have tested several of our key platforms on various hydrogen blends. For us, the combustion recipe is not all that difficult. Most of our gas and dual fuel engines can handle hydrogen blended with natural gas up to about 20%. There is still more work to do to better understand the impact on long term component life, safety factors, and the obvious economic considerations. We are working to develop a 100% hydrogen engine for electric power generation, but the end-use markets are not very mature yet given the lack of affordable hydrogen gas. That said, we understand hydrogen combustion and the related engine component technologies very well. When the demand for hydrogen engines evolves, we will be ready.”
Caterpillar and many other OEMs have successfully blended hydrogen with natural gas. The industry will have trouble advancing and using hydrogen in real-world applications until there is a readily available supply. Given the industry is still years away from this goal, it makes sense why interest for hydrogen blending was more popular a few years ago than it is today. However, the hydrogen supply chain is improving.
After more than a year of deliberation, the US Department of Energy selected seven regional hydrogen hubs that will split US$7 billion in funding as a result of the Bipartisan Infrastructure Law. Collectively, the hubs aim to produce more than 3.31 million tons (3 million tonnes) of clean hydrogen per year, achieving nearly one-third of the 2030 US clean hydrogen production goal of 11.02 million tons (10 million tonnes). Through technological strides and scale, the hubs should help to reduce the cost of green hydrogen production. Together, the seven Hydrogen Hubs will eliminate 27.56 million tons (25 million tonnes) of CO2 emissions from end users each year — an amount roughly equivalent to combined annual emissions of more than 5.5 million gasoline-powered cars (see “Hydrogen Report: Seven For Seven,” December 2023 Gas Compression Magazine, p. 34).
Fulfilling Customer Demand

Caterpillar is ramping up its supply chain to meet the need for G3600 A4 Gen 2 new engine orders, as well as Gen 2 upgrade kits. “We’re focused on launching the product, the supply chain availability, and meeting customer demand,” said Bohlmann. “Some of our customers may prefer to keep their fleet consistent and may not introduce new hardware right away. We are working with customers to assess adoption rates, and I expect they will be quite high. The product is on the shelf at our parts distribution centers, so parts are available within days. Now, if there’s a sharp increase in order volume, that may change, but we are monitoring sales closely and will be able to adjust to customer needs.”