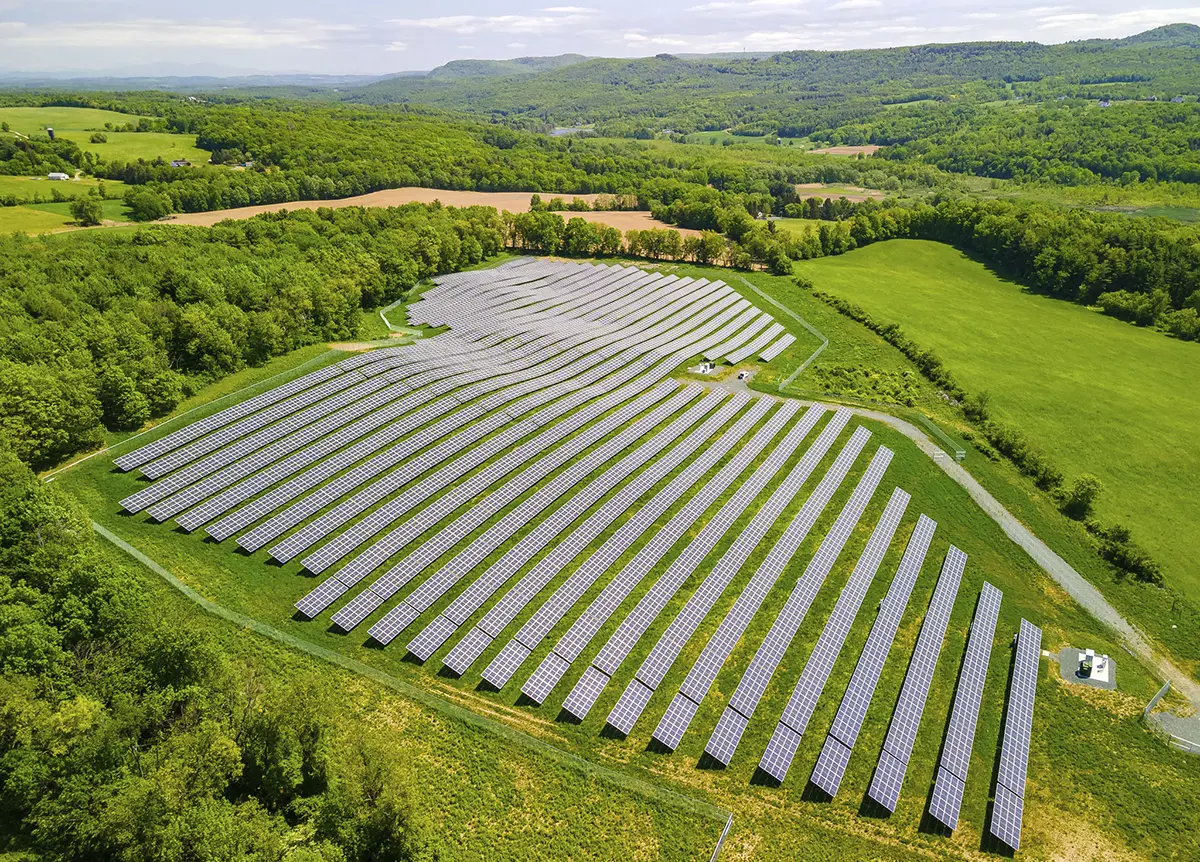
GTI Energy And US Steel To Demonstrate Industrial Carbon Capture Technology
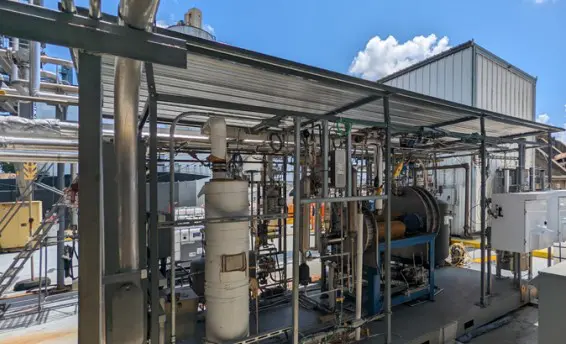
GTI Energy has been selected for new funding from the US Department of Energy (DOE). GTI Energy will demonstrate its ROTA-CAP carbon capture technology at US Steel’s Edgar Thomson facility in Braddock, Pennsylvania. The project will assess the readiness of carbon capture technology for commercial scale-up and widescale deployment.
“GTI Energy is not merely testing innovative carbon management solutions, we are demonstrating their real-world viability and economic potential,” said Don Stevenson, vice president of carbon management and conversion at GTI Energy. “This partnership will showcase the power of collaboration and innovation in tackling the complex challenge of transitioning to cleaner energy systems.”
ROTA-CAP is a modular, scalable carbon dioxide (CO2) capture process that combines compact rotating packed bed (RPB) technology with advanced solvent technology. According to GTI Energy, ROTA-CAP’s rotation of the packing in the RPB increases the mass transfer between the contacting fluids (the flue gas and the CO2 capture solvent), leading to a highly compact capture system with lower capital expenditures, while opening the door to the application of advanced, low-energy solvent systems that are beyond the operating capabilities of conventional solvent columns.

In ROTA-CAP, an advanced solvent is fed into the RPB absorber through the inner radius and flows to the outer radius. The CO2-rich flue gas stream is introduced into the absorber from the outer radius and flows toward the inner radius, contacting the solvent in a counter-current flow process. The rotation around the axis generates a centrifugal force that is significantly greater than the gravitational force in a conventional packed bed column.
GTI Energy’s ROTA-CAP has undergone extensive system-level, proof-of-concept, and performance validation testing at the National Carbon Capture Center. The skid-mounted system has been successfully operating for more than 1600 hours under various real flue gas conditions including coal, natural gas-fed power plant flue gas, and a range of typical industrial flue gas compositions. Solvent was provided by Carbon Clean. Supported by the DOE, the development has leveraged GTI Energy’s experience in RPB process technology for natural gas dehydration and acid gas removal.
“Lowering carbon emissions in our operations is a key part of the US steel strategy,” said Scott Buckiso, senior vice president and chief manufacturing officer at US Steel. “We welcome the collaboration with the DOE and GTI Energy at our Edgar Thomson plant, together we’re creating solutions that will shape the future.”
The DOE’s Carbon Management Market Liftoff Report estimates that the US needs to capture and store 400 to 1800 million tonnes of carbon dioxide annually to meet its 2050 decarbonization goals. Industrial sectors such as steel and cement production contribute significantly to global CO2 emissions, typically at large individual point sources, and are considered hard to decarbonize.