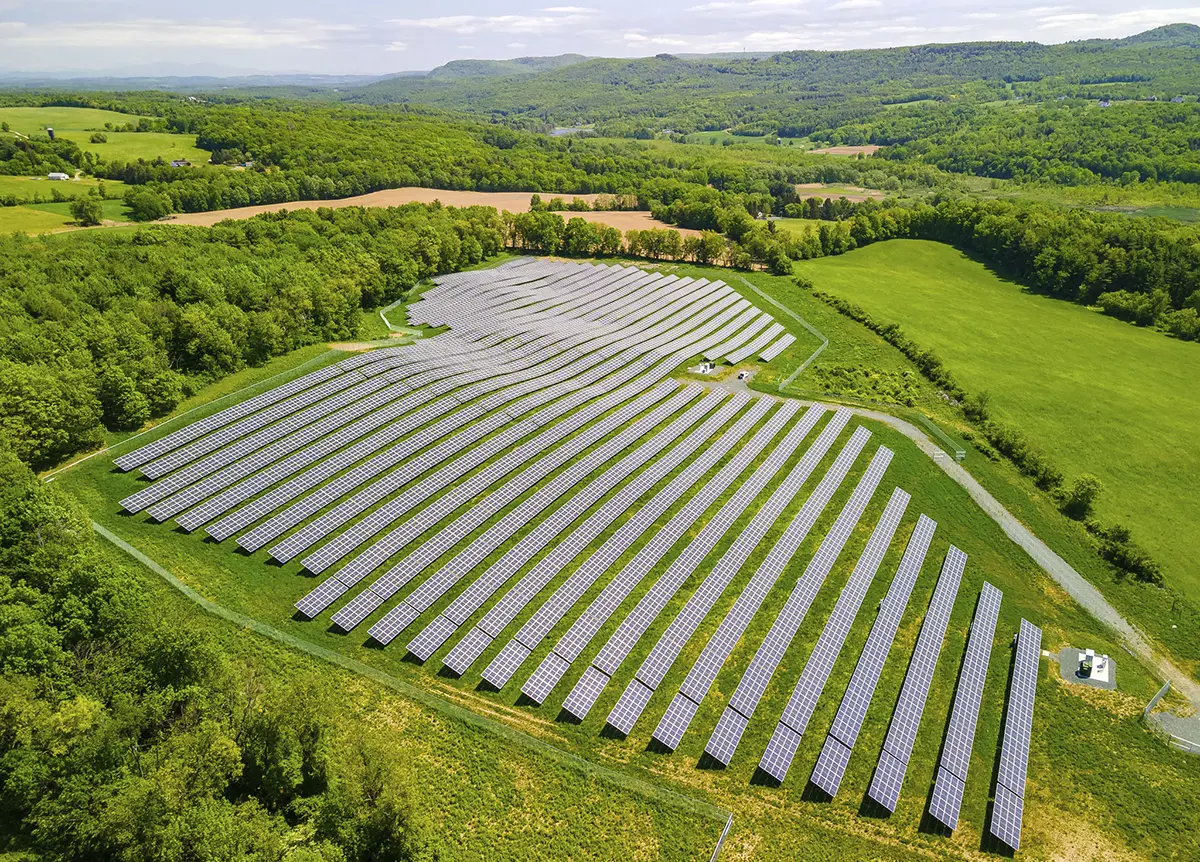
Anax Power Turns Compressed Gas Into Clean Energy
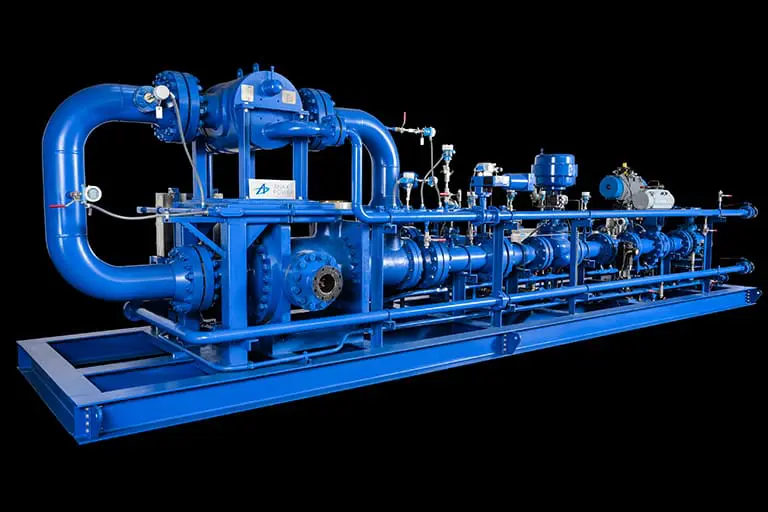
By Drew Robb
Anax Power (Anax) has completed commissioning of its ATE-500 Turboexpander at a pressure regulating station in Johnsonburg, Pennsylvania. This is the first turboexpander installation on a natural gas pipeline in North America in over 20 years.
Anax developed the ATE-500 as a novel way to repurpose excess pressure in natural gas regulating stations to generate clean electricity. Once gas traverses through the pipeline network to its destination point, the pressure is typically too high. It needs to be brought to a usable level, which is traditionally done using pressure regulating valves such as Joule-Thomson (JT) valves. JT valves cool the gas and reduce its pressure.
The 670 hp (500 kW) ATE-500 turboexpander is installed in parallel with the pressure regulating valve. It uses the change in pressure to spin a turbine within the turboexpander system. This process expands the gas and uses the waste energy to generate clean power, but the energy needs to be put to work.
“That power is there to be used in the most financially attractive and environmentally favorable way, whether that be in a data center, electrolyzer, behind-the-meter, or putting it onto the electric grid,” said Joe Longo, chief executive officer of Anax. “The system uses waste heat in the pressure letdown process, which may allow the ATE to offset existing scope 1 emissions on site.”

How The ATE-500 Works
When a gas is expanded, it cools. This happens whether the gas goes through a valve or a turboexpander. With the Anax turboexpander, usable work is extracted as you expand the gas and spin a turbine. The system generates power from natural gas without combustion using the pressure and flow of the gas moving through pipelines to spin the turbine. It’s a similar process to wind spinning a turbine. This carbon-free source of energy harnesses energy wasted in the natural gas regulation process to create financial and environmental value for power plants, pipeline operators, and large industrial users of natural gas and electricity.
As the gas cools, however, this can sometimes pose a problem for pipelines as they need to keep the gas above freezing to avoid damage. Line heaters are typically used to warm the gas after it is expanded. However, they are inefficient, burn valuable natural gas, and emit carbon dioxide (CO2). Although many sites do not need additional heat, additional heat can be captured as waste heat from Anax’s data center systems and brought to the site.
“At some locations, our turboexpander may overcool the gas, and heat needs to be added to the gas flow,” said Longo. “Doing that using inefficient line heaters would impair the system’s net power output and environmental footprint. Our solution is to pair the turboexpander with a data center which produces an enormous amount of waste heat with much higher efficiency than line heaters.”
The ATE-500 is capable of operating at a pressure regulating station that has an inlet pressure above 400 psi (27 bar), a pressure ratio (inlet pressure/outlet pressure) above 1.2, and mass flow above 12 MMscf/d (339,802 m3/d). The higher the pressure ratio, the less flow is required to generate full power output.
The turboexpander has an operating speed of 15,000 rpm and can handle fluctuating pressures and flows. Inlet pressure ranges from 400 psig to 1200 psig (82 bar) with a pressure ratio of 1.2 to 3.4. It includes components such as an Allen Bradley Wonderware Intouch SCADA interface, an electrical panel from Longo Electrical-Mechanical, an interstage heater from Vahterus Plate and Shell (30% Glycol) of Finland, a turbine designed by SoftInWay, magnetic bearings from Waukesha Bearings, and a generator from Turbo Power Systems. Everything is mounted on one skid with a length of 30.9 ft. (9.4 m), a width of 7.6 ft. (2.3 m), and a height of 8.3 ft. (2.5 m).
Longo called out SoftInWay as a critical partner in moving from prototype to a fully commercial product.
“SoftInWay assisted in optimizing the turbomachinery in the system and integrating the turbomachinery with the balance of plant,” he said. “They understood our need to build a system that was not only technically functional, but economically viable.”
Valentine Moroz, chief operations officer at SoftInWay, explained that Anax first approached his company about five years ago with a goal to generate clean power from natural gas without any combustion using a turboexpander generator. SoftInWay AxSTREAM software was used for the design of turbomachinery and related thermal-fluid systems. An initial feasibility study determined relevant natural gas parameters and proposed the optimal turboexpander configuration. Hydraulic analysis helped to refine specifications for valves, flow meters, heaters, and pipes. Computational fluid dynamics analyses optimized turbine flow paths and generator cooling. A rotor axial thrust balancing mechanism was developed to minimize loading on the active magnetic bearing. Rotor dynamics and thermal expansion analyses, as well as structural evaluations, were also performed.
“The vision was to utilize the pressure and flow of natural gas moving through pipelines to spin the turbine and generate power,” said Moroz.
The result is a two-stage expansion design to increase control of gas flow and maximize the amount of energy that can be extracted from the gas stream. An axial flow turbine with a partial admission design includes a direct-drive generator, without the need for a gearbox. Active Magnetic Bearings (AMBs) bring stability and eliminate cross contaminating gas and oil.
This machine has been performance and safety tested by the Gas Technology Institute (GTI) and offers a 25- to 30-year lifespan. The entire turboexpander is pre-assembled, requiring minimal pipework or electrical wiring on site. Optional remote monitoring and remote emergency stop facilities can be added.
Only the 670-hp unit is currently available, which can be derated down to 335 hp (250 kW). The company selected the 670-hp size after speaking to many potential customers and surveying the market. The results were plotted by inlet pressure and pressure ratio. Anax then drew a box around the customers it wanted to serve. The optimum system size was determined to be 670 hp.
“If there is a site with more flow, Anax can stack multiple turboexpanders in-parallel to build a larger system,” added Longo. “While ATE-500 was designed for natural gas transmission companies, Anax plans to bring to market a second-generation, 335 hp turboexpander that will focus on serving local distribution companies.
Technology Demonstration
Turboexpanders may be commonplace in cryogenic plants, air separation plants, and liquefied natural gas facilities, but they have not gained much traction in natural gas pipelines. A big reason for this lack of adoption on pipelines is that most turboexpanders were designed for controlled facilities where the pressure and flow do not change. A controlled environment means the turboexpander can be engineered to the specific process conditions in the plant, without a need to handle significant variation. Natural gas pipelines, however, cannot be classified as controlled environments. The pressure and flow can fluctuate on a minute-by-minute basis. Thus, traditional turboexpanders do not perform well in such volatile environments where the efficiency can fall off as operating conditions move away from the turboexpander design point. In contrast, the ATE-500 is designed to handle volatile natural gas conditions and perform efficiently across a range of natural gas conditions.
In 2017, Anax tested its prototype on the national grid system in the United Kingdom. After review, GTI said, “…the performance and safety tests conducted at the DNV-GL Flow Centre, in accordance with a test plan and corresponding test results, indicate technical feasibility and safe operation of the Anax-Star ASTE250 GLG [the Anax Turboexpander].” Since then, the focus has been on engineering refinement to improve overall economics.
As additional validation, a grant from Emissions Reduction Alberta funded a study on the potential value from the ATE-500. Its findings based on the 2022 Grid Emissions Factor for the province of Alberta: 3723 MWh of annual carbon-free power per unit, 0.57 tonnes CO2e/MWh emissions reduction, and 2124 tonnes CO2e annual emissions reduction per unit. These numbers will vary from location to location.
Many years of research and engineering work have finally borne fruit. In July of 2024, after several intermediate testing procedures, Anax has commissioned an ATE-500 unit in a pressure regulating station in Johnsonburg, Pennsylvania, in partnership with Pin Oak Midstream. Longo believes North America hasn’t seen such a turboexpander installation on a natural gas pipeline in more than two decades.
The turboexpander is designed to be installed at the end of a pipeline, where gas is expanded to a usable end-level, whether that be at a city-gate, large customer delivery, power plant, or other pressure drop location. At regulating stations, for example, the unit is connected on the upstream and downstream side of the pressure regulating station with either an open flange or by cutting into the existing headers. There is generally plenty of room at pressure regulating stations for at least one ATE-500.