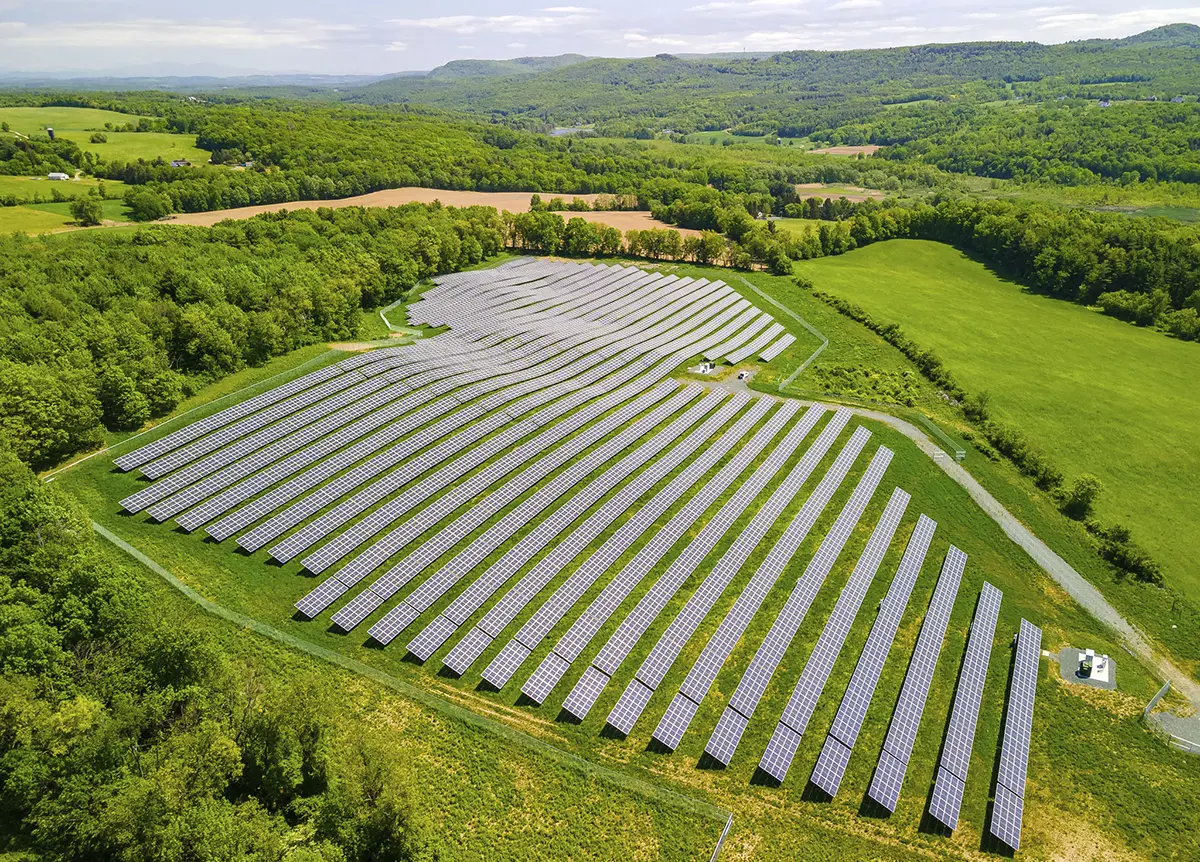
2028’s Hydrogen Dream Team: Part 1
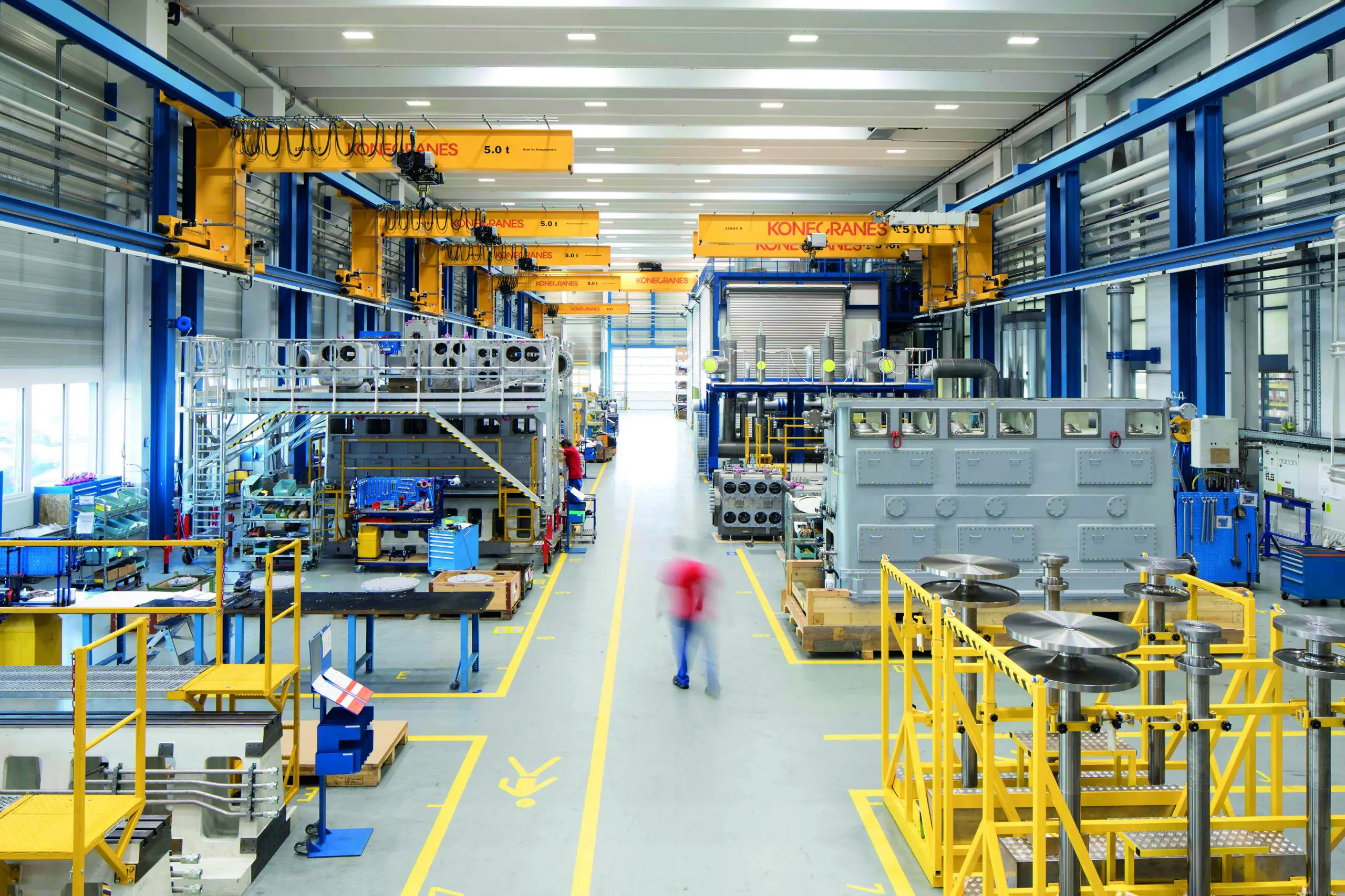
US-based venture capital and private equity firm, Insight Partners, released its Hydrogen Compressor Market Report. In the report, Insight Partners identifies Neuman & Esser Group (NEA), Atlas Copco, and Burckhardt Compression (Burckhardt) as top leaders that are shaping the future hydrogen compressor market. In Part 1 of “2028’s Hydrogen Dream Team,” we’ll discuss the leading role that hydrogen compressor manufacturers have on shaping the hydrogen (H2) economy and some noteworthy compressors on the market by major original equipment manufacturers (OEMs). In Part 2, we’ll discuss political support for hydrogen compression, where the market could be headed, different types of hydrogen compressors and their use cases, hydrogen fuel cells, and which geographic regions hold the most promise for the H2 economy.
The Importance Of Hydrogen Compressor Manufacturers
The global hydrogen compressor market can be broken in different types, stages, and end users. The two types are typically oil-based and oil-free compressors, which can be single-stage or multistage. End users include chemical, oil and gas, automotive and transportation, renewable energy, and other companies. Currently, the oil and gas industry is the largest end user. Surprisingly, renewable energy is already the second largest end user, followed by the chemicals industry, automotive and transportation industry, and then other end users.
Hydrogen’s claim to fame is that it is abundant and has one of the highest energy contents per weight. The issue is that its density is just 90g per m3 under atmospheric conditions (normal pressure and temperature conditions), meaning it must be compressed to achieve usable levels of energy density. Pressure varies based on the task at hand. On the low end, less than 3600-psi (250-bar) pressure is required to compress high quantities of oil-free hydrogen. If oil traces are permitted in the gas, discharge pressures can exceed 9000 psi (600 bar) with lubricated compression.
Hydrogen compressors can even reach extremely high pressures of more than 75,000 psi (5000 bar). One such example is NEA’s diaphragm compressors, which ensures oil- and leakage-free compression. These compressors operate best under continues load. NEA also makes hydraulic-driven, dry running piston compressors for volatile operating scenarios that require small amounts of hydrogen. These compressors can reach pressures of up to 45,000 psi (3000 bar) and offer oil-, leakage-, and abrasion-free compression. NEA offers integrated solutions along the hydrogen value chain, including the production and usage of hydrogen.
“The oil and gas and chemical industries experience tremendous growth across the world; moreover, various renewable energy projects are in the pipeline, especially in Southeast Asian countries,” said the Insight Partners report. “Thus, the requirement for better-conducting channels in various industries is offering future growth opportunities for the global hydrogen compressor market. The current growth of the hydrogen compressor market is primarily attributed to the introduction of advanced products by the hydrogen compressor manufacturers.”
A Growing Industry
Since 1975, international demand for hydrogen has increased by more than 300%. Hydrogen has traditionally been used in industrial processes, oil refining, and ammonia industries. Today, it is increasingly being sought after for fuel cell applications, mainly in transport cars, and as a method for storing renewable energy. However, the vast majority of hydrogen is currently supplied by fossil fuels. An alternative method for hydrogen production is through water electrolysis, which is the process of separating hydrogen from water. In layman’s terms, it involves shocking the water so the positive hydrogen molecules separate from the negative oxygen molecules.
Electrolysis has been around for more than 100 years, but methods and technology are improving. “Hydrogen has a very high energy content per weight, but unfortunately not by volume,” said Alexander Peters, managing partner of the NEA Group. “Therefore, it is necessary to compress the hydrogen to achieve the required energy density. Nonlube piston compressors, with their high efficiency, are able to compress hydrogen up to 350 bar [5100 psi] while ensuring the trailer fills up to around 300 bar [4400 psi]. Increased transport demands for hydrogen will lead to higher discharge pressure that will likely come from pipeline filling and transport compressors operating up to 100 bar [1500 psi]. In order to have an energy buffer to compensate for the volatility in the renewable energy sources like wind and photovoltaics, cavern storage at up to 200 bar [3000 psi] will be a core application for piston compressors. Here, we are talking about possible volume flows of up to 125,000 scf [200,000 m3] of hydrogen per hour at 30-bar [450-psi] suction pressure, requiring around 16-MW drive power. The leakage-free diaphragm compressors on the other side, now and in the future, are mainly used for higher pressures and lower mass flows. They are well suited to fulfill the compression needs for power to gas [PTG] and hydrogen refueling stations [HRS]. The trend seems to be that 700-bar [10,200-psi] tank pressure will become the standard for refueling vehicles. Diaphragm compressors can also serve bigger end users like entire truck or bus fleets with the required mass flows,” said Alexander Peters.
Although hydrogen compressor manufacturers rely on raw materials providers, parts, components, their own integrated supply chains, government bodies, industry associations, and regulatory agencies, it is ultimately up to the manufacturers to develop the technology and products needed for the distributors and end users to implement the infrastructure that ultimately advances the H2 economy.
Burckhardt And Atlas Copco Take Commanding Roles In Hydrogen Compression
In addition to NEA Group, Burckhardt and Atlas Copco stand out as two major compressor manufacturers that are investing in the global hydrogen compressor market. In August 2021, Burckhardt announced it would deliver three process gas compressor API 618 systems to South Korea for hydrogen compression at what is expected to be the largest hydrogen liquefaction plant in the world.

South Korea is currently a leader in hydrogen clean energy. To keep its pole position, it’s building a plant expected to produce up to 90 tons (81.6 tonnes) of hydrogen per day starting in 2023. The three compressors, including auxiliaries, have a shaft power of 6.6 MW per compressor. The compressors will be used in parallel for higher liquefaction capacity and to increase the pressure of the supplied hydrogen from atmospheric pressure up to 841 psi (58 bar). Burckhardt Compression offers a comprehensive hydrogen compressor portfolio for a variety of hydrogen applications. According to Burckhardt, its piston compressor technology stands for the highest hydrogen purity and longest mean time between overhauls.
Insight Partners called out Atlas Copco’s heavy duty gas compressors as a meaningful product that’s impacting the hydrogen compressor market. Atlas Copco’s CU oil-lubricated, high-pressure, heavy-duty gas compressors offer efficient compression of air, nitrogen, natural gas, hydrogen, helium, and other industrial gases. This compressor line is mainly used in high-pressure applications such as natural gas vehicle refueling stations, hydrogen refueling systems, bottle filling, and air-blast circuit breakers.
In March 2022, Atlas Copco will celebrate its 149th anniversary as a company. Founded in 1873 in Stockholm, Sweden, to manufacture equipment for the railway industry, the company has become a world benchmark in the supply of air and gas compressors, industrial gas generators, equipment for air quality treatment, power tools, assembly solutions, quality assurance products, transportable compressors, generator sets, lighting towers, specialized rental, and related services. Today, Atlas Copco has 40,000 employees and a global reach with customers in more than 180 countries in industries such as food and beverage, pharmaceutical, metallurgical, textile, petrochemical, automotive, electronics, aeronautics, construction, and oil and gas, among others.
Over the last few years, Atlas Copco has undergone a noticeable expansion, part of which can be attributed to its decentralized approach. Aside from organic growth, acquisitions have played a major role in fueling Atlas Copco’s support for new markets outside of Sweden. In the first nine months of 2021, Atlas Copco acquired 15 companies across a variety of industries. It then made at least four more acquisitions in the last three months of 2020.
Most of its acquisitions were for compressed air distributers and service providers. It’s rare to see a company of Atlas Copco’s size making such frequent and specific acquisitions. Over half of the companies Atlas Copco acquired in 2021 had less than 20 employees. While it’s uncertain how niche companies in specific markets will integrate into a company the size of Atlas Copco, the acquisitions fall in line with the company’s strategic approach to growth.